1. Нанесите моторное масло на внутреннюю
часть нового маслоотражательного колпачка клапана. |
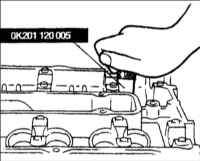 | 2.
Установите маслоотражательный колпачок клапана на направляющую втулку клапана
с помощью специального приспособления ОК201 120 005. |
3. Установите нижнюю тарелку клапана. |
4.
Установите клапан. |
| 5. Установите пружины клапана и верхнюю тарелку
клапана. |
6. Установите пружину
клапана таким образом, чтобы витки с мелким шагом (В) были направлены к головке
блока цилиндров. |
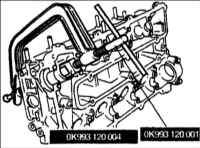 | 7.
Установите верхнее гнездо пружины и специальным приспособлением сожмите пружину. |
8. Установите сухари и снимите специальное
приспособление для сжатия пружины. |
9.
Пластиковым молотком несколько раз ударьте по торцу стержня клапана для того,
чтобы сухари установились на свои места. |
10. Повторите эти операции на всех клапанах. |
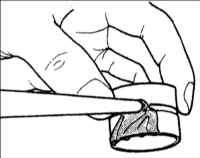 | 11.
Нанесите тонкий слой моторного масла на боковую поверхность гидравлических
компенсаторов зазоров клапанов. |
12. Установите
гидравлические компенсаторы на те места, откуда они были сняты. |
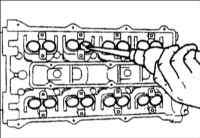 | 13.
Проверьте, нет ли свободного перемещения гидравлических компенсаторов. |
14. Тщательно удалите с верхней части блока
цилиндров все загрязнения и масло. |
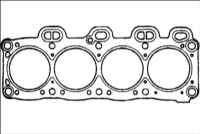 | 15.
Установите новую прокладку головки цилиндров. |
16.
Установите головку цилиндров. |
17.
Нанесите моторное масло на резьбы болтов и поверхности седел. |
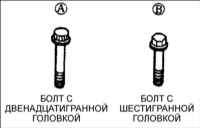 |
Предупреждение
Убедитесь, что болты головки цилиндров одного типа – (А) или (В). Не используйте
болты разных типов вперемешку.
|
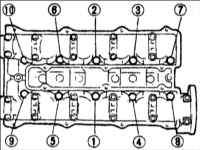 | 18.
В определенной последовательности затяните болты крепления головки блока цилиндров
в следующем порядке. FE DOHC: 80–86 Н•м Т8 DOHC: а. затяните болты
моментом затяжки 49 Н•м; b. в последовательности, обратной затягиванию, ослабьте
болты; с. затяните болты моментом затяжки 39,2Н•м; d. доверните болты
на угол 90°. |
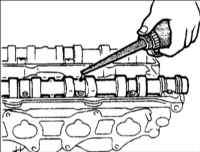 | 19.
Нанесите достаточное количество моторного масла на шейки и подшипники распределительных
валов. |
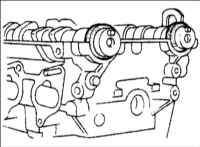 | 20.
Установите распределительные валы так, чтобы установочный штифт располагался точно
вверху. |
21. Нанесите достаточное
количество чистого моторного масла на контуры кулачков и шейки распределительных
валов. |
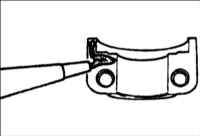 | 22.
Нанесите силиконовый герметик на привалочные поверхности передних крышек распределительных
валов. |
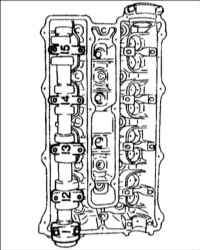 | 23.
Установите крышки распределительных валов в соответствии с их номерами и разметкой. |
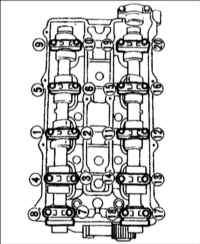 | 24.
В определенной последовательности за 2–3 этапа затяните болты крепления крышек
распределительных валов. Момент затяжки: 17,6–26,5 Н•м |
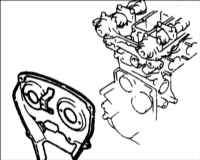 | 25.
Установите уплотнительную пластину и закрепите ее болтами. Момент затяжки:
7,8–11,8 Н•м |
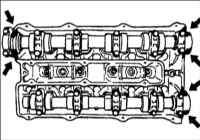 | 26.
Нанесите силиконовый герметик на передние и заднюю крышку распределительных валов. |
27. Установите крышку головки цилиндров и
закрепите ее болтами. Момент затяжки: 3,9–5,9 Н•м |
28.
Удалите грязь и смазку с поверхности корпуса датчика угла поворота. |
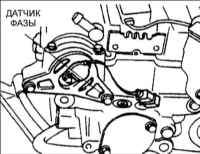 | 29.
Установите датчик угла поворота с новым уплотнительным кольцом и закрепите его
болтами. |
Предупреждение
Не используйте повторно
уплотнительное кольцо.
|